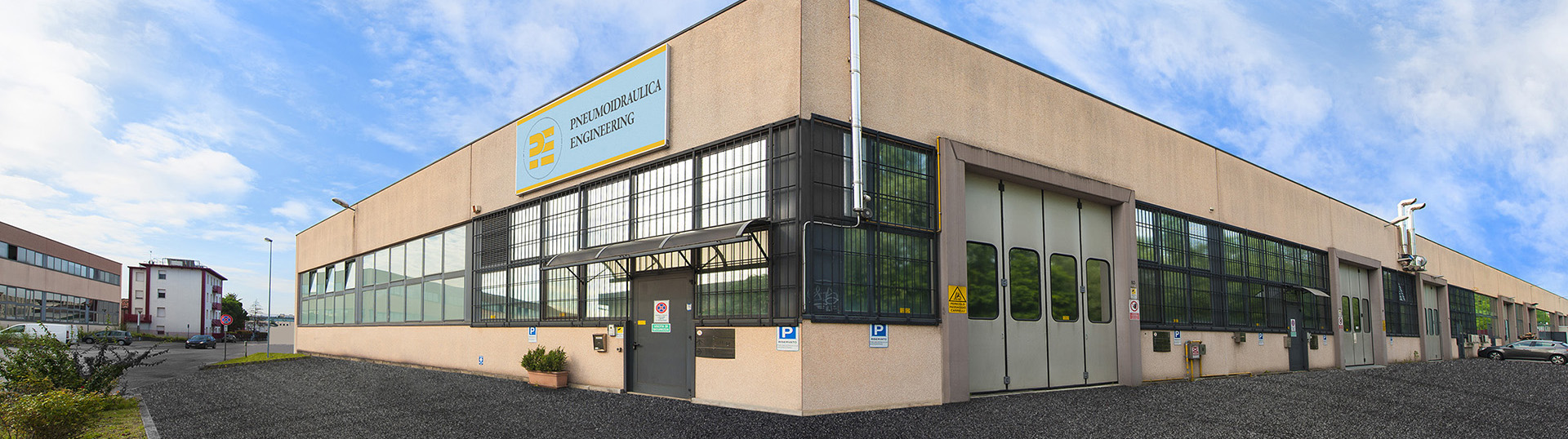
Our strength?
Provide control systems with a quality and reliability at the highest levels on the market!
Innovation, spirit of enterprise and technical challenges were the main elements that characterized the birth, in 1994, of PNEUMOIDRAULICA ENGINEERING. The goal, to provide high quality products for Oil & Gas.
Still today PNEUMOIDRAULICA ENGINEERING is on the market not as a dealer but as a designer, manufacturer, installer and provider of maintenance of pneumatic and hydraulic control and safety systems.
Our long experience in the field, thanks to the multi-year service activity (both on-shore and off-shore) and the plants direction, assures us a precise and continuous training, essential for the design of new plants. PNEUMOIDRAULICA ENGINEERING is authorized as a “Metric Operator” for the calibration and the repair of the fiscal measuring equipment.
The company is certified according to
ISO 9001:2015 (download the certificate)
ISO 14001:2015 (download the certificate)
ISO 45001:2018 (download the certificate)

Mission:
Constantly achieve the highest quality in order to supply our customers with high quality and reliability products at a competitive price giving an excellent technical assistance and consultant services differentiating ourselves from the competitors.
Raise awareness among our potential customers. If they invest in the high quality of our product they have an initial cost which it will be extensively recovered thanks to the absence of anomalies and shutdowns.

Integrated Quality, Safety and Environment Policy:
Our Policy establishes the general objectives to be achieved and the commitments to achieve them, both in relation to external needs (improvement of the performance of its products/services, customer satisfaction, socio-economic needs) and in relation to the internal needs (satisfaction of the internal staff, reduction of non-conformities).
PNEUMOIDRAULICA ENGINEERING distinguishes itself towards its customers in the field of:
- Design, Assembling, Installation, Maintenance and Technical Assistance of pneumatic-hydraulic components and control systems for the oil & gas
For years, we have decided to improve our organization, to reduce the impact of our activities on the surrounding environment, as well as the risks associated with carrying them out.
To this end we propose, in compliance with current laws, to operate according to a Quality, Environment and Safety Management System in compliance with the reference regulations.
Responsibility for managing the System concerns the entire company organization, from the Employer to each worker, each according to their own duties and responsibilities.
The objectives defined are:
- fulfillment of the requirements (requested by the Customer and necessary to comply with the requirements of the services), including the applicable mandatory ones;
- continuous improvement of the effectiveness of the management system;
- reduce costs, eliminating the internal non-conformities and those caused by external Suppliers;
- make resources individually responsible: valuing the work done by both managers and their collaborators;
- constantly monitor resource consumption in order to minimize it;
- constantly monitor the risks highlighted in the Risk Assessment document;
- continuously improve and prevent pollution: in particular by managing in a controlled manner the activities that can produce waste water, emissions into the atmosphere, etc.;
- manage the waste produced directly or indirectly;
- consider everything concerning the environment and safety as the same of the other management aspects of the company and of the customer needs.
In view of the aforementioned objectives, the organization has identified and defined the commitments to achieve them in terms of tools, methods, resources and anything else necessary to ensure their achievement.
The main commitments include:
- consider Safety and Health in the workplace and the related results as an integral part of the company management;
- provide the necessary human and instrumental resources;
- the awareness and training of workers regarding the safe performance of their duties in order to assume their responsibilities in terms of safety and health in the workplace;
- the involvement and consultation of workers, also through their safety representatives;
- the periodic review of the Policy itself and of the Management System implemented;
- the definition and dissemination within the Company of the objectives of Safety and Health in the workplace and the related implementation programmes.
The tools to achieve these objectives are:
- The maintenance of appropriate "Internal Audit" procedures: working to prevent, or in any case promptly remove, causes of discrepancies with respect to both the characteristics of the Service and the times and costs agreed with the Customer;
- Training/Training: introducing all corporate functions at all levels to the disciplines of Quality - Environment and Safety and in particular to those in positions of responsibility;
- The maintenance of a company management system according to the UNI EN ISO 9001:2015, UNI EN ISO 14001 and UNI ISO 45001 standards: these are reference standards for the Organization;
- Organization: defines the organizational chart and organizational objectives of all the Functions.
The tools identified as necessary to achieve one's objectives affect the entire organization in an integrated corporate vision and in a correct balance, with all the aspects that contribute to outlining corporate strategies.
Download Integrated Quality, Safety and Environment Policy document in PDF format

History:
1994-1996
The activity is mainly devoted to the research and development of a pneumatic control valves seal system able to fully satisfy the Oil & Gas severe requirements. We realized the revolutionary metal-to-metal system (without wearing parts) still provided today with success thanks to its unsurpassed reliability qualities and a lifetime warranty.
1997-2000
The study and production of AISI 316 stainless steel hydraulic control valves starts. It also starts the production of the first excess flow valves suitable for fusible plugs network and for compressed natural gas (CNG) stations.
2001-2005
It starts the production of the first Well Head Control Panels (WHCP) for off-shore application. It also starts the production of the first sampling systems. The company increases employees and it moves in new larger premises.
The direct cooperation with ENI starts and thanks to the award of a multi-year on-site service agreement, we are present in all the Italian treatment and compression gas stations. Further people enters in the staff and, thanks to a new fleet of vehicles and equipment, the “Service Division” starts activity.
We start the production of new products (pneumatic pressure switches, fusible plugs) able to satisfy ENI’s requirements for strategic applications.
2006-2010
The company moves into the new premises of Via dell'Edilizia, within a new industrial complex. In 2008 the warehouse and the shop are enlarged in order to meet the continuous production of gas sampling and control systems and the company reaches the ISO 9001 certification from BSI.
A new ERP system is implemented with the aim to automatize the production process and new highly specialized professionals enters into the staff. It starts the plants direction activity and the cooperation with Nuova Pneumatica S.r.l., a company founded in 2009 by the same partners of Pneumoidraulica Engineering, which designs and manufactures compressed air skids.
2011-2015
They are signed new distribution agreements with foreign partners thus increasing export quota. In contrast with competitors, the stock availability is greatly increased in order to offer more and more products for immediate delivery.
A special technical department starts the study and the realization of compatible spare parts for pneumatics and hydraulics over all the industrial fields.
Today
The research and development department has been equipped with an innovative 3D printer that allows us to easily create the prototypes of the new components thus accelerating the setup before the final realization.
The new e-commerce web site www.inoxtubefittingsshop.it for the direct sale of our stainless steel AISI 316 components is on line. With an availability of over 22000 articles, it arises between the best stocked in Europe and the challenge for our team is to be able to fulfill all the orders within 24 hours.
Download Integrated Quality, Safety and Environment Policy document in PDF format
